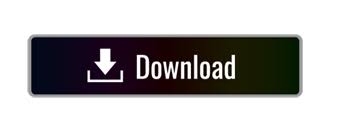
- #WATER ROCKET SIMULATION SOFTWARE FREE DOWNLOAD PLUS#
- #WATER ROCKET SIMULATION SOFTWARE FREE DOWNLOAD SERIES#
#WATER ROCKET SIMULATION SOFTWARE FREE DOWNLOAD PLUS#
System Reliability and Safety Analyses plus Fault Data Analytics Furthermore, the new inverter leg model (one phase) lets you create custom inverters easily and quickly.
#WATER ROCKET SIMULATION SOFTWARE FREE DOWNLOAD SERIES#
Electro-Mechanics model library: Simulate and analyze torque ripple as a source of noise or vibration excitation caused by discrete controllers for electric drivetrains. In an effort to foster hands-on, inquiry-based learning in science and math, the NASA Glenn Research Center has developed a series of interactive computer programs for students.Highlights of this release New: Simulation of Switched Controls for NVH Analyses You can also extend SimulationX with your own application-specific libraries or integrate SimulationX into your CAE world via interfaces, such as FMI®, Executable Model or our many XiL interfaces.

Based on the open model description language Modelica®, SimulationX comes with many predefined model libraries that can be used out-of-the-box. For this purpose it will be needed to design and develop a measuring system for evaluation of pressure and temperature inside the rocket, and the level of the water in the rocket. Identify and optimize the parameters with the biggest influence on the system behavior and design new concepts. SimulationX allows you to fully analyze the interaction between your system’s parts, components and assemblies (subsystems). As a single platform for modeling and analyzing dynamic system behavior, you can use it in various engineering fields. The results can offer theoretical references for calculation of the jet flow field with water spray, and have vital guiding significance for the water cooling system design.ESI’s SimulationX® provides you with state-of-the-art technology in physical system simulation. The rigorous thermal environment of the rocket afterbody is improved after injecting water with a large angle. With the increases of the spray angle, the peak temperature in impingement surface gradually decreased and maximum reduction is 17.84%.
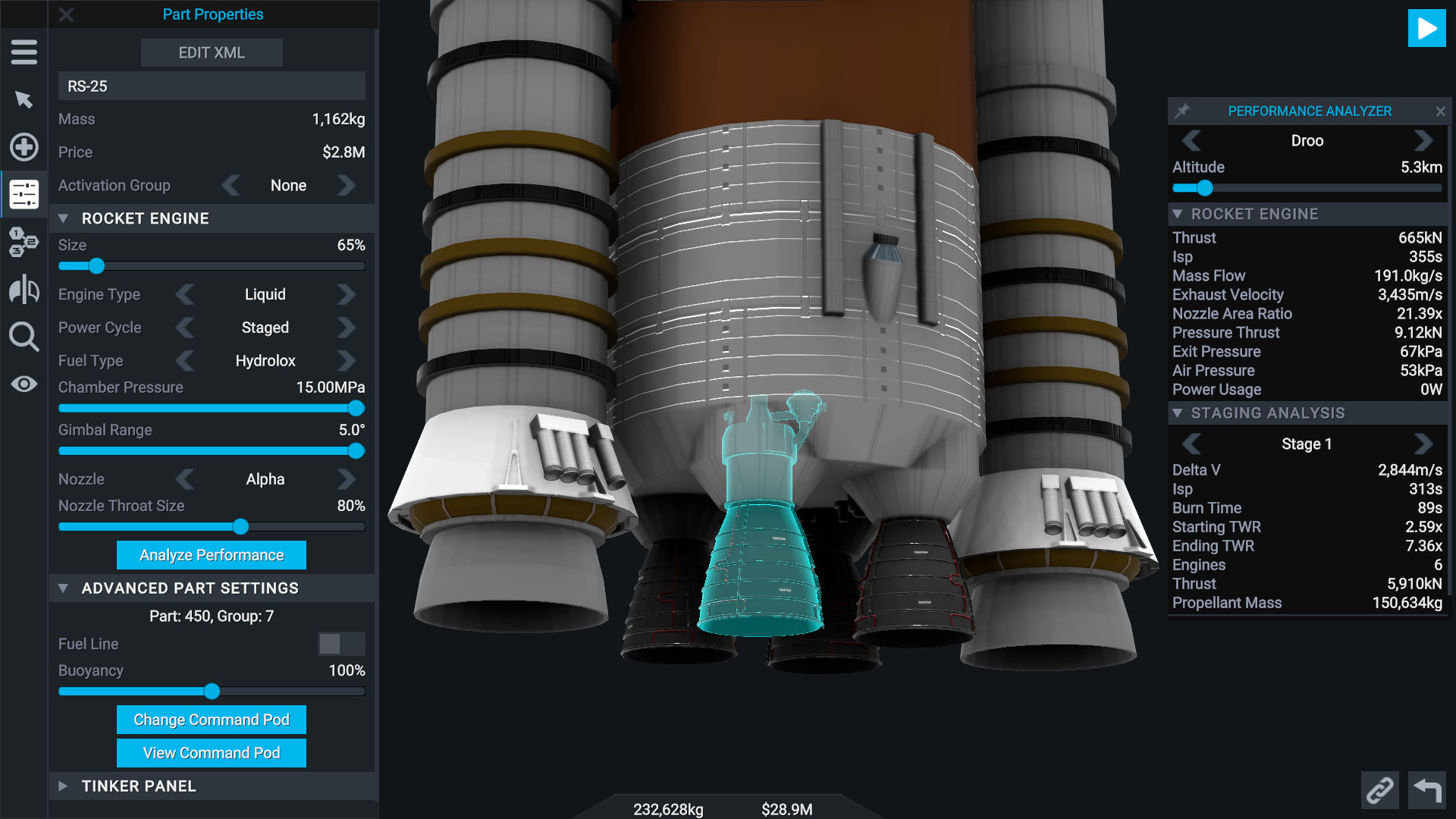
The temperature of the impingement plate has a significant dropped after spraying water, by approximately 450 to 750 K. Meanwhile, the stability of the jet flow could be affected by large spray angles. The water spray has an obvious cooling effect on the impingement plate with increasing of the injection angle. The results show that the afterburning mainly occurs in the mixing layer between the exhaust plume and air. Then, the jet flow fields under different water spray angles are calculated. The comparison between numerical results and experimental data confirms the validity of this model.

The evaporation and condensation of the water flow are simulated by using the Eulerian dispersed phase (EDP) model. It is an advanced object-oriented, non-linear thermodynamic modeling environment used by the aerospace industry for modeling turbomachinery, air-breathing propulsion systems, liquid rocket engines, engine control systems, and system model. To investigate the effect of afterburning and water injection on the thermal environment of the rocket jet flow, three-dimensional hybrid RANS/LES method and a nine-species and ten-step chemical mechanism are used to establish the thermodynamic model of the exhaust plume. Numerical Propulsion System Simulation (NPSS) N PSS ® stands for Numerical Propulsion System Simulation.
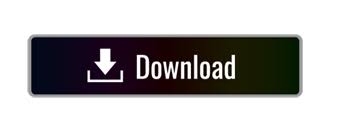